Unique High-brilliance X-ray Sheds New Light on Additive Manufacturing Process
October 27, 2017
By Holly Jordan, AFRL Materials and Manufacturing Directorate
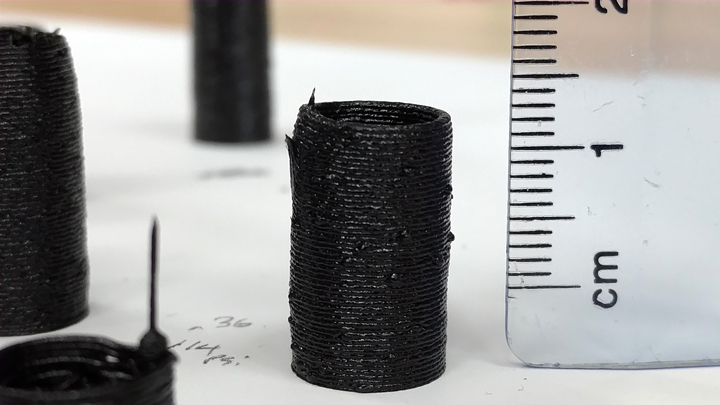
The additive manufacturing process involves depositing thin layers of composite materials on top of each other. AFRL Composite Materials and Processing team researchers used the ultra-bright X-ray at the National Synchrotron Light Source II at Brookhaven National Laboratory to gain better insight into the bonding of composite layers during the additive manufacturing process. (U.S. Air Force photo/Harry Pierson)
The following feature story originally appeared on the Wright-Patterson Air Force Base website. It describes how researchers with the Air Force Research Laboratory's Materials and Manufacturing Directorate are improving 3-D printing. The research team used beamline 11-ID at the National Synchrotron Light Source II (NSLS-II)—a U.S. Department of Energy Office of Science User Facility located at Brookhaven Lab—to study the structure of 3-D-printed materials in real-time during processing. For more information, contact Ricarda Laasch, 631-344-8458, laasch@bnl.gov.
WRIGHT-PATTERSON AIR FORCE BASE, Ohio – AFRL Materials and Manufacturing Directorate researchers recently took advantage of a unique and rare research opportunity to better understand the behavior of materials used in the additive manufacturing process.
Once a little-known curiosity, the popularity of additive manufacturing, or 3-D printing as it is commonly known, has increased in recent years, both among researchers and home hobbyists. The technology can easily be used to create a wide variety of common and not-so-common objects. It’s no surprise, then, that the military is interested in putting this versatile technology to use for the warfighter.
The additive manufacturing process involves depositing, or “printing,” thin layers of material on top of each other, following a pattern and slowly building until the layers form a complete solid object. AFRL researchers are interested in using this technology for a variety of purposes, including to quickly and inexpensively produce non-critical replacement parts in the field.
The technology, however, is not yet mature enough for practical warfighter use. The complication arises in the way printed layers keep their shape when bonding to each other. Material porosity and other factors such as weak blending can result in poor bonding between layers, weakening the overall structure of the additively manufactured component.
To address this problem, in addition to reinforcement fillers, researchers add nanofillers to the composite medium to act as flow and setting (rheology) modifiers, and to aid in overall structural bonding. In common terms, the resulting behavior can be compared to that of toothpaste, which flows easily under pressure but doesn’t drip or flow when at rest. The precise amount of nanofiller, when added to a reinforcement filler such as carbon fiber, will greatly improve the mechanical properties of a printed part. Therefore, understanding the material properties and dynamics of different mixtures of composites and nanofillers is an important step in making additive manufacturing technology more practical for common use.
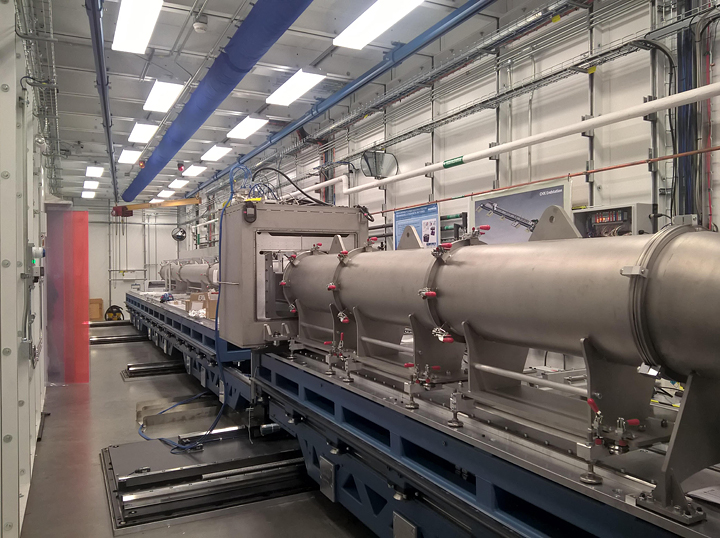
The AFRL Polymer Matrix Composite Materials and Processing team was granted the opportunity to work in collaboration with beamline scientists at the National Synchrotron Light Source II at Brookhaven National Laboratory, allowing them the opportunity to gain an unprecedented view into the behavior of additive manufacturing materials and processes. (U.S. Air Force photo/Hilmar Koerner)
To advance the body of knowledge in this topic, AFRL researchers identified and made use of a unique research opportunity to gain an unprecedented view into the behavior of these materials. Materials scientist Dr. Hilmar Koerner of the Polymer Matrix Composite Materials and Processing team was granted the opportunity to work in collaboration with beamline scientists at the National Synchrotron Light Source II at Brookhaven National Laboratory, allowing the team to conduct real-time experiments and gather unique data.
“We were awarded beam time at the XPCS [X-ray Photon Correlation Spectroscopy] beamline, which allows us to simultaneously look at the dynamics and structure of materials during processing with millisecond time resolution,” said Koerner. He said that the team used their beam time to pass the ultra-bright X-rays though the roads and layers of deposited material, allowing real-time information to be gathered on the alignment and dynamics of the nanofiller.
Koerner explained that when the composite ink exits the 3-D printing nozzle, it turns from a shear-thinned, easily flowable liquid into a gel within just a few seconds. As the nanofiller particles randomize their orientation, they form a network that gives the composite ink self-supporting properties (similar to toothpaste). The XPCS experiment allowed the researchers to understand this fast process in great detail, providing information that can help optimize both the composite inks and the printing process as a whole for better performance.
The National Synchrotron Light Source II is a unique facility that allows researchers from academia and industry to take advantage of extremely bright X-rays for analytical research purposes. To be able to use the equipment, researchers must submit a proposal identifying the nature of their research, the need to use the equipment, and a description of the experiments to be conducted. The proposal is then peer-reviewed, and a decision is made regarding allotment of equipment use.
“We were excited to find out that we had been granted beam time at this unique beamline. We conducted our experiments and gathered data that will allow us to better characterize these materials and shed some light into the 3-D printing process of Air Force-relevant thermosetting resins and their post processing,” Koerner said.
The team will use this newly-gathered data to optimize composite ink formulations and printer parameters. Koerner says that correlating this data with other, simpler characterization methods can provide a number of benefits to the team’s in-house research efforts, including new closed-loop feedback controls for 3-D printers and a new ability to characterize AFRL-developed materials that experience much higher temperatures during printing.
2017-12588 | INT/EXT | Newsroom