Cabling for LHC Upgrade Wraps Up
Experts at Berkeley Lab finished winding more than 2000 kilometers of superconducting wire into cables for new magnets that will help upgrade the Large Hadron Collider and the search for new physics
August 30, 2023
The following story was originally published by the U.S. Department of Energy’s (DOE) Lawrence Berkeley National Laboratory. It describes the first step of making the superconducting coils for magnets at the Large Hadron Collider (LHC). Scientists from DOE's Brookhaven National Laboratory play multiple roles in the research at the LHC, including contributing to the design of the niobium tin magnets described in this feature, winding and heat treating the coils, and testing the magnets. For more information about Brookhaven's roles in the high-luminosity LHC upgrade, contact Karen McNulty Walsh, kmcnulty@bnl.gov, (631) 344-8350.
By Lauren Biron, Berkeley Lab Science Writer
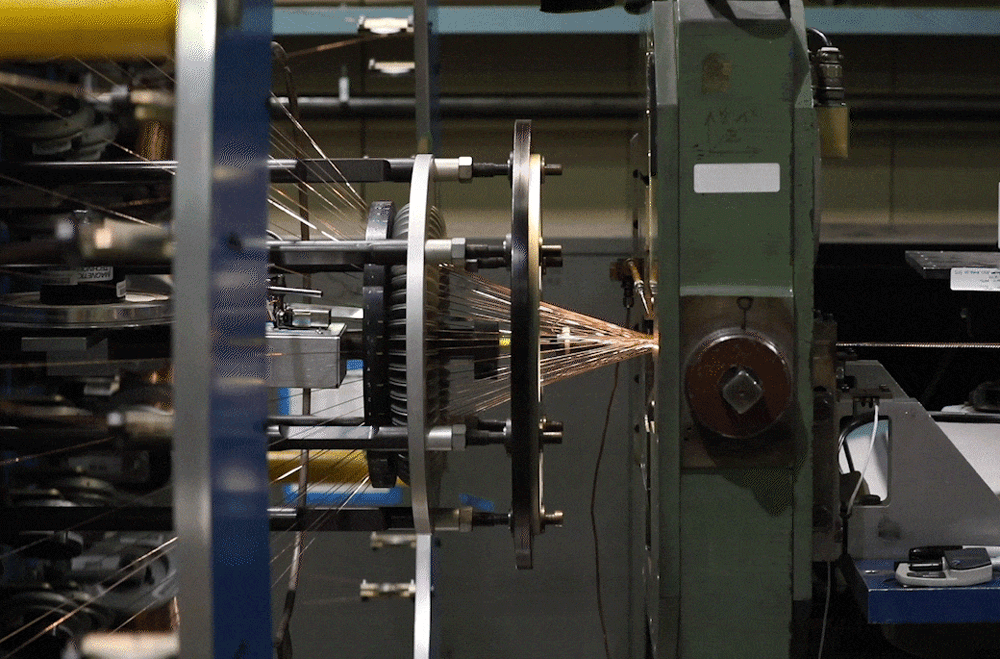
Berkeley Lab has finished winding wire into the cables needed to make focusing magnets for the Accelerator Upgrade Project. (Credit: Marilyn Sargent/Berkeley Lab)
To better understand how our universe works, researchers are upgrading the most powerful particle accelerator in the world: the Large Hadron Collider (LHC). Today, a team at the Department of Energy’s Lawrence Berkeley National Laboratory (Berkeley Lab) completed a crucial step in the upgrade, turning more than 2220 km (1367 miles) of wire into cables for the next generation of focusing magnets at the LHC.
The magnets will be the most powerful of their kind and vastly increase the number of collisions in the LHC’s two general purpose detectors, ATLAS and CMS. More collisions produce more data, meaning scientists can better search for rare and undiscovered phenomena and investigate some of the biggest mysteries in physics – things like the origin of mass and the nature of dark matter and dark energy.
“Superconducting magnets enable the science produced at the LHC, and we have an outstanding multi-lab team pushing the frontiers of magnet technology,” said Soren Prestemon, director of the Berkeley Center for Magnet Technology. “For the first time, we will be utilizing the extraordinary properties of niobium-tin superconductor in an operating collider.”
The first step in making those magnets is turning superconducting wire into cables that can then be wound into magnet coils. But making those cables is no easy feat. Each one of the 111 cables is a single, continuous piece made by wrapping 40 individual strands of wire around a stainless-steel core. If even one wire crossed over another anywhere along the entire length – typically 470 meters – the cable would be ruined. The effort required collaboration from experts in Berkeley Lab’s Accelerator Technology & Applied Physics (ATAP) Division and Engineering Division.
“We are like a director of a ballet company,” said Ian Pong, a staff scientist in ATAP who leads the cabling task. “We have 40 dancers – the wire spools – pirouetting in a circle through the run of about three hours, and our responsibility is to make sure that no single missed step happens during the entire performance.”
Making the cables is one part of the Accelerator Upgrade Project (AUP), the U.S. contribution to the High-Luminosity LHC (HL-LHC) project. Four institutions collaborate to design, produce, and test the magnets for AUP: Berkeley Lab, Brookhaven National Laboratory, the National High Magnetic Field Laboratory at Florida State University, and Fermi National Accelerator Laboratory, which leads the project.
“While each step of the magnet building process is of equal importance, none of the other steps can happen without first having high-quality superconducting cables,” said Mike Naus, a scientific engineering associate in ATAP and the deputy task leader.
Since 2016, Berkeley Lab has been winding AUP cables and sending them on a months-long journey to becoming magnets. The cables are coiled and heat-treated at Brookhaven Lab and Fermilab before returning to Berkeley Lab, where four coils are assembled into magnets called quadrupoles. At Fermilab, quadrupoles are joined together in “cryo-assemblies” that are tested and shipped to CERN, where they will be installed during a long shutdown of the LHC later this decade.
“These are very high-tech pieces of equipment that involve people from all around the U.S.,” said Jean-Francois Croteau, a postdoctoral researcher in ATAP who worked on quality assurance of the cables. “It’s impressive to have all these labs involved to create something that none of them could make alone.”
Making the new magnets out of niobium-tin allows for larger magnetic fields than in any previous magnets made of niobium-titanium. The magnets will operate at roughly 12 tesla, several hundred thousand times stronger than the Earth’s magnetic field. They’ll work in concert with a longer version of quadrupole magnets that are currently being produced by CERN (where the superconducting cable winding is 70% complete).
Together, the focusing magnets will squeeze the LHC’s particle beams into dense bunches, increasing the chance that particles will interact. Once upgraded, the High-Luminosity LHC will be able to produce between 5 and 7.5 billion proton collisions per second (compared to the current 1 billion), and scientists expect to produce at least 15 million Higgs bosons per year.
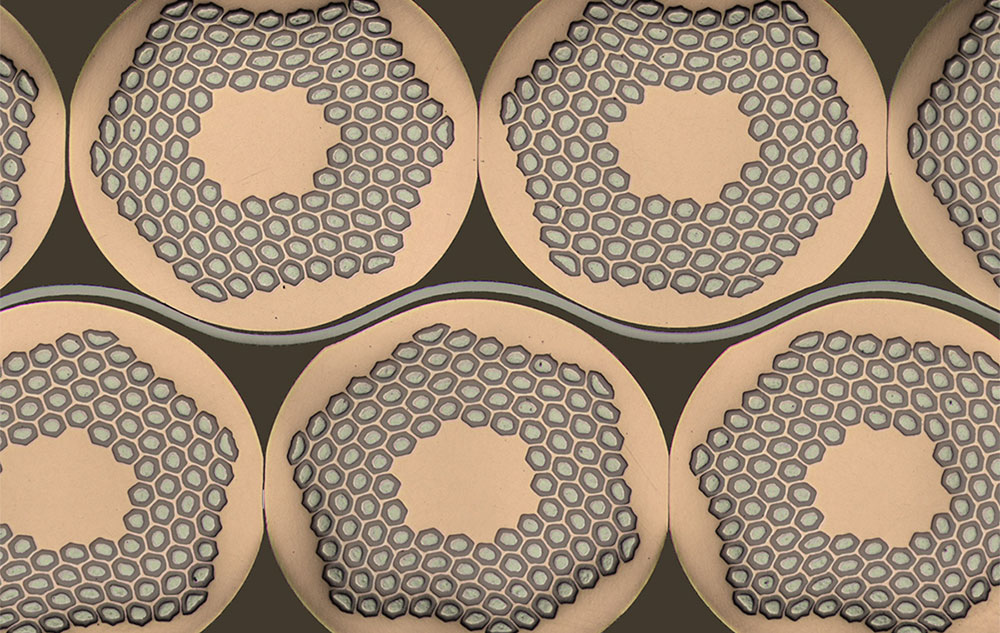
Each wire contains niobium and tin, separated by copper. When heat-treated, the superconducting niobium-tin is formed.
Making the perfect cable
Not far from the cabling machine are stacks of pizza boxes with barcodes. Each one holds a sample from a cable – a record of what has been produced and one of the many elements of quality control. The Berkeley Lab team used a combination of cameras, microscopes, and electrical and mechanical tests to ensure the cables met their exacting specifications. For example, the thickness over the entire length of the cable could vary by no more than 10 microns in either direction, about one-tenth the width of a human hair.
Every cable began life as a bundle of chaotic wires that technicians combed into order. After inspecting a qualification sample, the team would begin the 3-hour, non-stop cabling run.
“We wanted all the excitement during the pre-checks and outside of the cable runs,” said Andy Lin, a scientific engineering associate in ATAP who leads the cabling technical operation for the project and has operated the machine since 2015. “During production, we could make micro-adjustments, like moving the machine head a thousandth of an inch – but any action we take during the run is a risk, so we tried not to unless we had to.”
Twenty feet down the line, cameras imaged all four sides of the flattened cable along the entire length, making sure no wires crossed. Checking each cable takes almost 50,000 images, or roughly 5 million across AUP.
Over the life of the project, researchers learned more and more about the cabling machine, and how small changes could make subtle differences in the final cable. Something as simple as where lubrication was applied to the wires or whether an office fan was aimed at the machine could influence the end product. They also made improvements, such as speeding up the code that analyzes the images to operate nearly in real-time.
“We’re advancing what is possible in building these new cables,” said Cameron Geddes, the director of ATAP. “While these magnets power a new generation of fundamental physics, the techniques we’ve developed during this project are a step towards even more powerful future accelerators.”
To form the cables, the twist of wire is shaped into a flat “Rutherford-style” cable, deforming the wire at the edges. To ensure the arrangement and integrity of the wires, researchers carefully cut off a section from the end of each cable for inspection and testing, including measurements at extremely cold (cryogenic) temperatures. Each sample was then archived in its pizza box, and the full spool of cable was safely packed and transported to the next stage.
While the cabling step for AUP is now finished, teams at the collaborating institutions continue to assemble the focusing magnets. Berkeley Lab expects to finish making the quadrupoles in 2025, and researchers plan to turn on the HL-LHC in 2029.
“The magnets for the Accelerator Upgrade Project are cutting-edge technology, and they start with the exceptional cables produced at Berkeley Lab,” said Giorgio Apollinari, Fermilab scientist and HL-LHC AUP project manager. “We still have more work to do, but this is a significant milestone on our way to the HL-LHC and the discoveries it may bring.”
This work is supported by the DOE Office of Science High Energy Physics program.
Founded in 1931 on the belief that the biggest scientific challenges are best addressed by teams, Lawrence Berkeley National Laboratory and its scientists have been recognized with 16 Nobel Prizes. Today, Berkeley Lab researchers develop sustainable energy and environmental solutions, create useful new materials, advance the frontiers of computing, and probe the mysteries of life, matter, and the universe. Scientists from around the world rely on the Lab’s facilities for their own discovery science. Berkeley Lab is a multiprogram national laboratory, managed by the University of California for the U.S. Department of Energy’s Office of Science.
DOE’s Office of Science is the single largest supporter of basic research in the physical sciences in the United States, and is working to address some of the most pressing challenges of our time. For more information, please visit energy.gov/science.
2023-21421 | INT/EXT | Newsroom