- Home
-
Divisions
Energy Systems Division
- Renewables and Grid Modernization
- Energy Conversion
- Geothermal Materials
Energy Storage Division
- In-situ and Operando Analysis
- Vehicle Technologies
- Grid-level Storage
- Center for Mesoscale Transport Properties
- Long Island Solar Farm
- NSERC
- People
- Org Chart

Energy Systems Division
Geothermal Materials Group
Anti-corrosion and Anti-fouling coating
The objective of this project is to develop the processing and synthesis technologies of coating materials providing corrosion-, abrasive wear-, and scale fouling-mitigations of carbon steel (CS)-based -heat exchangers, -wellhead pipes, and -steam separators, and aluminum (Al)-finned-air-cooling condensers, in geothermal power plants. If successful, CS- and Al-based components will improve the power plant’s economic factors, including considerable reduction of the needed capital investment, and decrease in the operations and maintenance costs through optimized maintenance schedules.
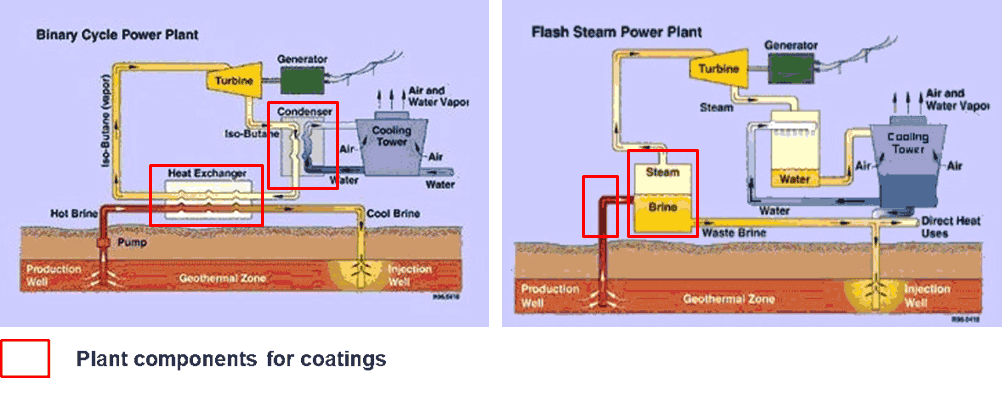
The following technologies were considered/developed:
- Semi-crystalline polyphenylenesulfide (PPS)-based coating technology was transferred to Curran International Corp. for commercialization.
- Self-assembling nano composite technology not only led to the fabrication of thin anti-corrosion Ce- and Sm-oxide/organometallic polymer (OMP) composite films on Al- and CS-based components, but also eliminated toxic Cr(VI) coating.
- Specific additives including micro-carbon fibers, nano-boehmite engineering ceramic, and calcium aluminate offered the improved thermal conductivity, abrasive wear resistant, tensile strength, elongation, and self-healing of semi-crystalline polymer coating.
- Exfoliated nano-clay composite technology provided the minimized hydrothermal oxidation and improved hydrothermal stability by increasing the melting point of thermoplastic PPS.
- Self-segregating molten blend polymer technology allowed designing slip, hydrophobic, anti-corrosion and –fouling coating.
- Developments of advanced 300oC-stable polyaryletherketone-type organic and Ti- or Zr- incorporated organometallic pre-ceramic composite coatings, and anti-cathodic delamination primers will be needed for further prolonging the lifecycle of high-temperature plant components and well casings.
-
Tatiana Pyatina
Energy Systems Division
Interdisciplinary Science Department
(631) 344-8646, tpyatina@bnl.gov