Meet Alessandra Colli: Engineering Improvements in 3-D-printed Metals
Colli seeks to merge materials risk analysis with data collected at world-class science tools to improve safety, reliability, and opportunities in metal additive manufacturing
December 3, 2019
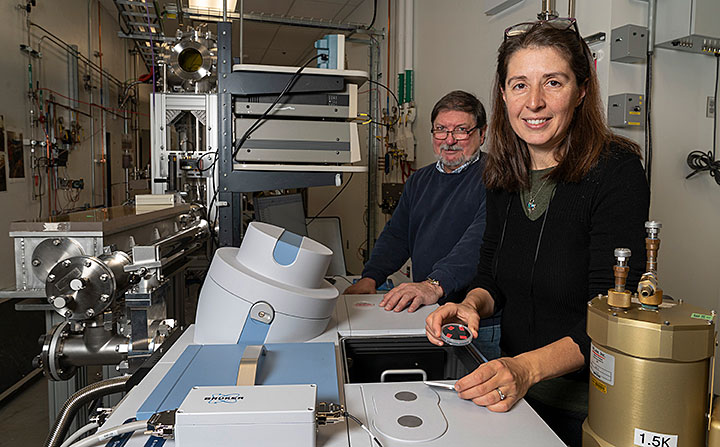
Alessandra Colli with National Synchrotron Light Source II beamline scientist Larry Carr at a beamline used for far-infrared spectroscopy (MET). This beamline will help characterize filter samples made by Obsidian AM, a company partnering with Brookhaven Lab to explore 3-D printing as a strategy for producing high-precision radiation filters for next-generation cosmic microwave background studies.
With a background in electrical engineering and risk assessment, Alessandra Colli, a scientist at the U.S. Department of Energy’s (DOE) Brookhaven National Laboratory, wants airplane engines to function flawlessly, rockets to be reliable, and a new telescope to be sensitive to signals that could solve secrets of the universe. Her focus, however, is not on the electronic circuitry that powers these complex devices, but rather on improving the structure and function of their many metallic components.
Colli is developing a strategy to leverage Brookhaven Lab’s materials-science capabilities and data analytics approaches to advance metal “additive manufacturing,” also known as 3-D printing. Compared with conventional metal manufacturing, 3-D printing offers great promise for building metal components with higher precision and greater reliability from the bottom up.
“When you are talking about reliability, most of the time you look at the system level—how the part performs in the field, in the real-world application,” Colli said. “We want to bring in the basic materials science—the kinds of studies we can do at the National Synchrotron Light Source II (NSLS-II) and the Center for Functional Nanomaterials (CFN) to look at material properties and defects at very small scales—along with analytical techniques being developed by our Computational Science Initiative to efficiently sift through that data.”
This approach could help scientists identify sources of material imperfections or weakness—and explore how different 3-D printing approaches or even new materials could improve a particular product.
“Industrial partners could come in and we can help them solve specific issues using the enormous capabilities of our DOE Office of Science user facilities,” Colli said.
3-D printed metals
Once used mainly for creating prototypes or models, additive manufacturing is moving into the mainstream for a range of industrial and defense applications, so much so that many industrial players address it as the next industrial revolution in manufacturing, Colli said. Using 3-D printing to manufacture precision metal engine components, high-tech filters, or even construction hinges and brackets offers ways to reduce waste of feedstock material and dramatically improve design to achieve better performance of the final product, she noted.
Instead of whittling down a larger block of metal, pouring molten material into a mold, or making separate components that must later be fastened together, 3-D printing uses a range of techniques to deposit the material layer by layer, printing only the desired object with little material wasted. The technology can create intricate objects and even allows construction from composite materials.
But to ensure durability, strength, resistance to corrosion, or other characteristics important for specific applications, it’s essential to understand not just what the manufactured part looks like and how it works in its application, but also what’s going on inside—the characteristics of the material itself.
Think about a piece that might be part of an airplane, or supporting parts for construction, part of a rocket engine or ship—these parts need extremely high reliability.
“With additive manufacturing, there can be different types of defects—residual stress that creates tension in an area where you may not want it; porosity formed by bubbles that create a weak spot where the part can break. We have a range of techniques that can see these structural characteristics and the materials’ chemical composition. And we can study them under different environmental conditions, like pressure or high heat, that when combined with certain material characteristics can cause a failure,” Colli said.
These tools can also help identify the best additive manufacturing processes for different applications, fine-tune manufacturing precision to take into account post-processing steps such as polishing or annealing, or explore new materials or combinations of materials that may improve functions.
Building collaborations
“There are lots of opportunities to grow collaborations with academic partners, industry, other departments at Brookhaven, and the user facilities here and at the other DOE Labs or research institutions around the world,” Colli said.
As an example, Colli notes one collaboration already underway among scientists in Brookhaven’s Sustainable Energy Technologies Department, Physics Department, Instrumentation Division, NSLS-II, and Obsidian AM (a small spin-off company from Yale University in Connecticut) that hopes to develop filters for cosmic microwave background radiation. These filters, designed for use in next-generation telescopes, are typically fabricated from metal as meshes or grids that get laminated together. Their job is to screen out signals from other forms of radiation so scientists can collect echoes of the radiation leftover from the Big Bang. Filtering out the “noise” will help physicists decipher details about neutrinos, dark matter, and general relativity.
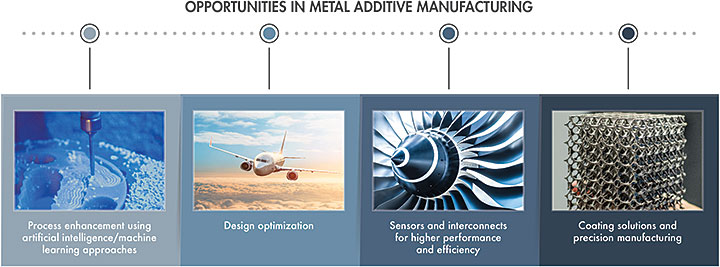
Scientific exploration of new materials, composites, and 3-D printing processes along with engineering studies of new applications will open many opportunities in metal additive manufacturing. This approach could guide the development of 3-D printed materials with reliability in harsh environments, reduced size and weight, or other characteristics optimized for specific applications.
“We are exploring plasma 3-D printing as a way to directly manufacture the full metamaterial for these filters. We’re starting by making sure we can print the metal part with optimal precision, but we are hoping to be able to print alternate layers of insulating material and metal grid directly using the same 3-D printing process,” Colli said.
This approach could be applied to making other layered metamaterials and composites, such as high-temperature superconductors (promising materials that carry electric current with no resistance) and magnets.
Colli is finalizing plans with professors at the North Carolina A&T State University and Rensselaer Polytechnic Institute to bring students in to learn about the various 3-D printing technologies, materials characterization tools such as x-ray diffraction, and approaches such as tensile stress testing. She is also collaborating with computational scientists to develop the tools and algorithms—many based on machine learning and other forms of “artificial intelligence”—to identify key indicators that will predict (and guide design to avoid) failure in additively manufactured metal components.
Varied background, open mind
“I’m not a materials scientist and I’m not a physicist, so to build this strategy and these collaborations, I had to learn everything too, including about the techniques; and I’m still learning,” Colli said. “My strength is to be able to understand both the small details and the big picture.”
Colli attributes her wide-scale vision to the diversity of topics she studied early in her career: electrical power engineering for her master thesis and risk analysis for her Ph.D., the former at the Polytechnic University of Milan in Italy and the latter at Delft University of Technology in The Netherlands. “Diversifying things gives perspective in terms of what you can learn and what you can see. It really opens up your mind,” she said.
She spent six years in The Netherlands developing methods to compare technological, environmental, and occupational risks of various energy technologies—fossil fuels, nuclear, and renewable energies such as solar. When she first came to Brookhaven Lab in 2011, she worked to integrate risk analysis into the economic side of evaluating energy systems.
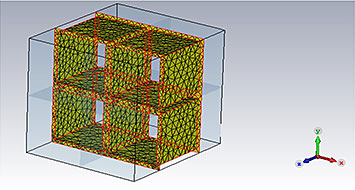
Simulations of filters for cosmic microwave background radiation telescopes help identify the best configuration for optimal performance. This graphic shows one layer of the copper configuration simulated using CST Studio Suite, a 3-D electromagnetic analysis software program. The simulation determines what types of radiation get transmitted through or filtered out by the mesh.
The proximity of the Northeast Solar Energy Research Center to NSLS-II first sparked her idea that understanding material properties might help address an energy challenge: why photovoltaic solar cells sometimes crack.
“My idea was to apply my knowledge in risk analysis to reliability issues in photovoltaics. What is the impact of the different materials that make up these layered structures on the tendency of cracks to form and propagate, for example? We have the solar panels and the synchrotron right here to do the materials science testing,” she said.
In 2018, Jim Misewich, Associate Laboratory Director for Energy and Photon Sciences (EPS), asked her to develop the Lab’s strategy for metal additive manufacturing as part of the EPS Growth plan. This opportunity gave her a chance to bring her idea of correlating material properties with performance and reliability to a new challenge.
“I had to grow in my career, to go from being a scientist doing my job in the lab to develop a leadership mentality,” she said. With support from the Growth Office—including Elspeth McSweeney, Michael Cowell, and Jun Wang—she developed skills and sought professional training courses such as the Women in STEM Leadership program at Stony Brook University.
“It was a year of enormous growth,” she said. “When people believe in you and they give you a chance, you feel obligated to give something back and to be successful. Supporting other people at the Lab helps us push each other.”
Meaningful mentorship
Colli puts these philosophies into practice as she mentors students through Brookhaven Lab’s Office of Educational Programs.
“For me, research is always about teamwork. I am not the boss and you are not my slave; we work together, period. It’s a continuous exchange,” she said. “I let the students bring up ideas—have them tell me what we should do.”
Sometimes suspicious of this approach and a bit lost without a predetermined path, Colli’s students often end up with an appreciation of what it means to be part of the scientific process.
“I don’t care if they do perfect work or not. But when I see that they get engaged and they get passionate, that’s for me the best reward.”
From her own experience, she also tells them, “Don’t be afraid if you end up in a different field because that may only increase your knowledge and open up your mind in different directions.”
When she’s not developing new strategies at the Lab, Colli loves to connect with nature by hiking and especially riding her horse. “That is where I find my peace of mind,” she said.
“I really love to be on Long Island, and I love the U.S.,” she added, noting that she hopes to become a full U.S. citizen as soon as she is eligible. “I still have two years to wait for that and I’m counting the days.”
The metal additive manufacturing strategy is supported by Brookhaven Lab’s program development funds. NSLS-II and CFN are DOE Office of Science user facilities. The Computational Science Initiative is also supported by the DOE Office of Science.
Brookhaven National Laboratory is supported by the U.S. Department of Energy’s Office of Science. The Office of Science is the single largest supporter of basic research in the physical sciences in the United States and is working to address some of the most pressing challenges of our time. For more information, visit https://www.energy.gov/science/
Follow @BrookhavenLab on Twitter or find us on Facebook
2019-16878 | INT/EXT | Newsroom