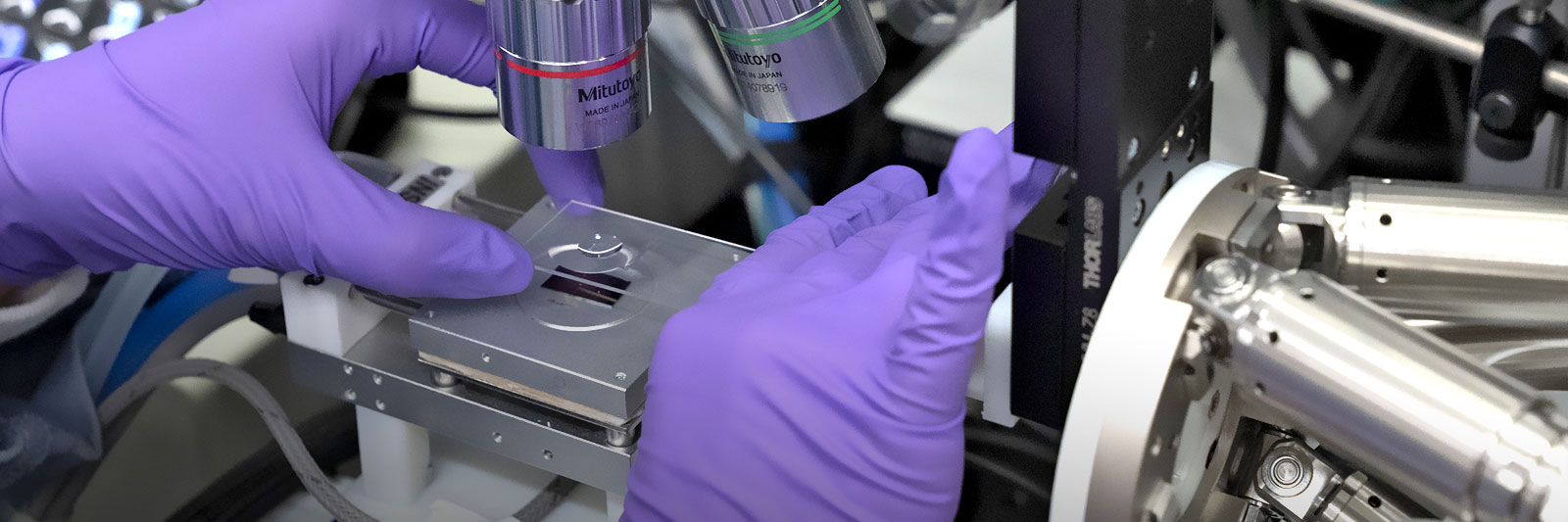
QPress Stacker
The stacker is a sophisticated robotic dry-transfer system designed for the precise handling and placement of exfoliated flakes using a polymer adhesive stamp.
A hexapod offers six-degrees-of-freedom (x, y, z, pitch, yaw, and roll) for complex motion control of a stamp during the approach, pressing, and detachment phases of the stacking process. Additionally, the substrate motion stage can move to select flakes of interest and rotating, which is crucial for fabricating layered moiré heterostructures. The system also features integrated heater (heated up to 300 °C) that accurately controls temperature during the transfer process and provides mild annealing.
Stage | Component | Description/Control |
---|---|---|
Sample Stage | XY-stages | res. 20 nm |
Rotation stage | ±155°, res. = 0.2 mdeg | |
Temperature control | room < T < 300° C | |
Lifting-pins | Robot loading / unloading substrates | |
Stamp stage | 6-axis stamp control | res. x = 0.8 um |
y,z = 0.2 um | ||
pitch = 0.28 mdeg | ||
yaw, roll = 0.14 mdeg | ||
z-stage | res. 0.10 um | |
Stamp gripper | Holding stamp | |
Microscope stage | Camera | 18MP color CMOS |
Camera focus (z) | Motorized stage, Super-long | |
Motorized nosepiece and objected lenses | Working distance lenses x5, x20, and x50 |
Status: The stacker is fully operational in Argon glovebox and currently accepting user proposals. This system is completely motorized and can be remotely controlled by an operator located outside of the glovebox, ensuring safety and precision in handling.
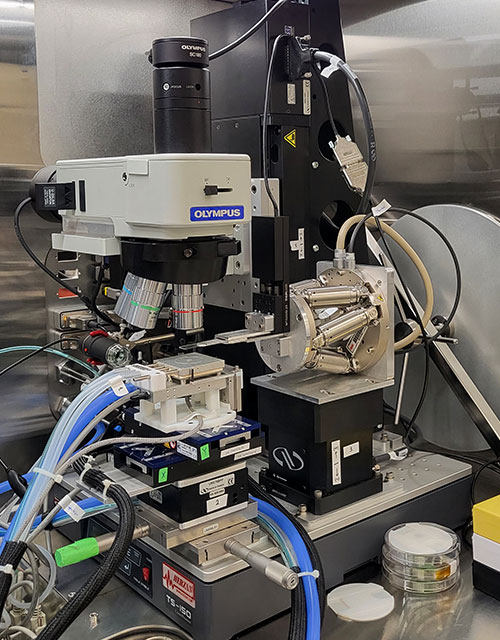
Stacker in glovebox
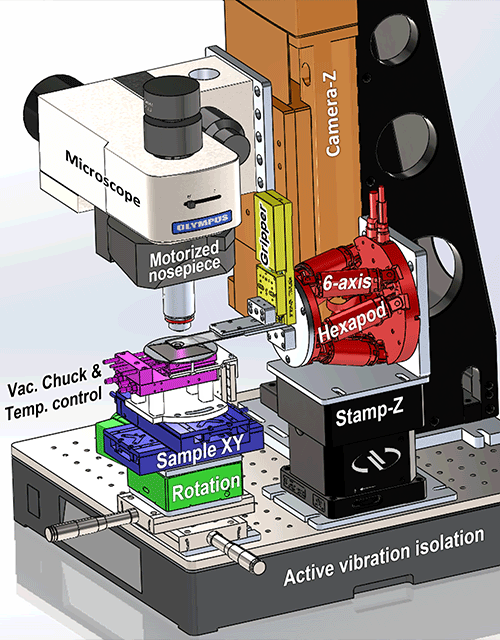
Stacker components
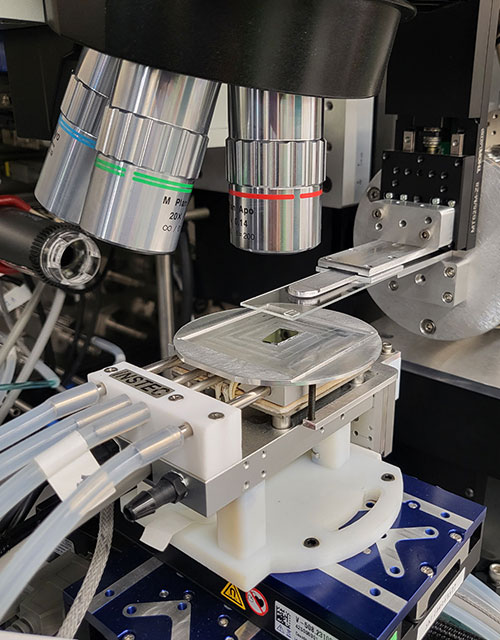
Closeup of Stacker microscope stage