About the Teams
Aprovecho Research Center
Cottage Grove, OR
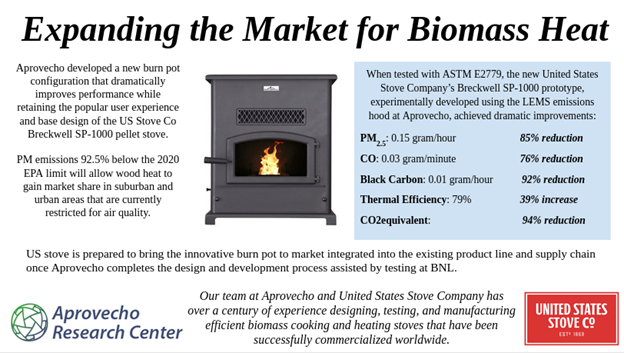
The Problem: Wood heating has the potential to produce large quantities of Particulate Matter which is dangerous to human health. This causes restrictions in wood heater usage and adoption in suburban and urban areas with poor air quality. Aprovecho believes dramatic improvements in wood heater performance will allow wood heat to gain market share in these areas and assure a future for wood heat in areas that are in curtailment.
The Technology: Aprovecho partnered with US Stove Company and took one of their proven, popular pellet heaters, the Breckwell SP1000 and retrofitted it with a novel burn pot, airflow configuration, and sensor package developed by Aprovecho. When tested by Aprovecho according to ASTM E2779, the prototype stove achieved 0.15 g/hr particulates, 0.01 g/hr black carbon, and 79% thermal efficiency, a drastic improvement with respect to EPA certification test results. Their iterative prototyping and testing process with real-time emissions monitoring resulted in a proprietary design that Aprovecho is seeking to patent.
The Team: The team consists of Nordica MacCarty, Ph.D. Executive Director of ARC and Assoc. Prof. of Mechanical Engineering at Oregon State University; Dean Still M.A., the Research Director at ARC; Sam Bentson, B.S. Aerospace Engineering, ARC Lab Manager; David Evitt, B.S. Mechanical engineering, ARC Program Manager; Ryan Thompson, MS Environmental Engineering, consultant; John Voorhees, VP of Compliance at US Stove; and Brandon Barry, VP of Engineering at US Stove.
Contact: Nordica MaCcarty, nordica@aprovecho.org. Web: http://aprovecho.org
Chimney Cherry
Los Angeles, CA
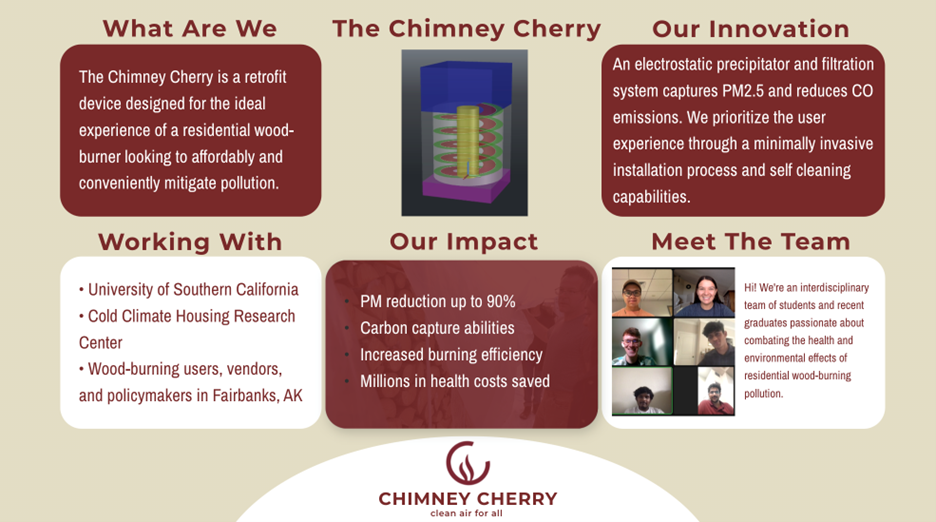
The Problem: The team conducted over a hundred hours of interviews and discovered many wood burners are reluctant or cannot afford to buy new heaters. According to the team, trade out programs haven’t achieved results because of the tradition of wood-burning and unreliable expensive electricity. However, the harmful health and environmental impacts of PM from residential wood burning cannot be denied.
The Technology: The Chimney Cherry is a unique electrostatic precipitator designed for people who don’t want to or cannot afford a new heater. It attaches to the rooftop chimney and is self-cleaning, allowing a user to continuously burn wood from October to March without having to clean the device. The team says “(they) are confident in (their) ability to reduce particulate matter by 90% and are testing (their) carbon capture and efficiency performance metrics. As an easier, cheaper, and emissions reducing device, the Chimney Cherry will revolutionize the residential wood-burning industry.”
The Team: The team began through a class at the University of Southern California. In the class the team focused on designing a product for Fairbanks, Alaska after discovering it’s the most polluted city in the US. Their team has expertise in filtration, public policy, marketing, and four engineering fields. Traction to date includes completing the Blackstone LaunchPad, NSF I-Corp’s ZAP! and BOOM programs, being a finalist in the USC Min Family Challenge, and a semi-finalist in MIT Solve.
Contact: Serena Allen, info.chimneycherry@gmail.com
Davidon Industries
Warwick, RI
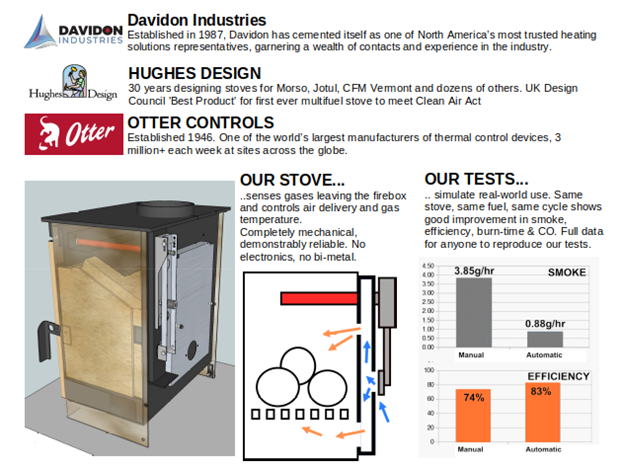
The Problem: When heaters are tested in labs, technicians can use their expertise and the prescriptive nature of the certification test methods to achieve low emissions, but average consumers do not have the same expertise or tools available. However, an automatic mechanical control, could theoretically replicate lab emission results, in a normal residential use situation.
The Technology: The Superstove heater is controlled by an invention - a purely mechanical, automatic combustion air control. The device is touted to be unique, compact, inexpensive, and easily adaptable to all sorts of wood heaters. The air control acts on the primary, secondary and tertiary air flows to tune the appliance to burn both efficiently and cleanly with no need for electricity or user input. The stove design itself made up of only 25 components when simple doors are used. All the replaceable parts slot into place, without the need for screws or clips, and the chimney can be swept through with no need for cleaning doors.
The Team: Davidon Industries represents leading manufacturers of internationally recognized and approved electro-mechanical and electronic controls and related materials. We specialize in the heater industry. Glyn Hughes is a wood heater specialist in the UK and has helped designed wood stoves for Morso, Jotul and Vermont Castings. Otter Controls has over 200 years of combined experience in thermostats and temperature controls and produce 3 million of them every week.
Contact: Adam McKnight amcknight@davidonindustries.com Web: https://davidonindustries.com/
Kleiss Engineering
Cloverdale, IN
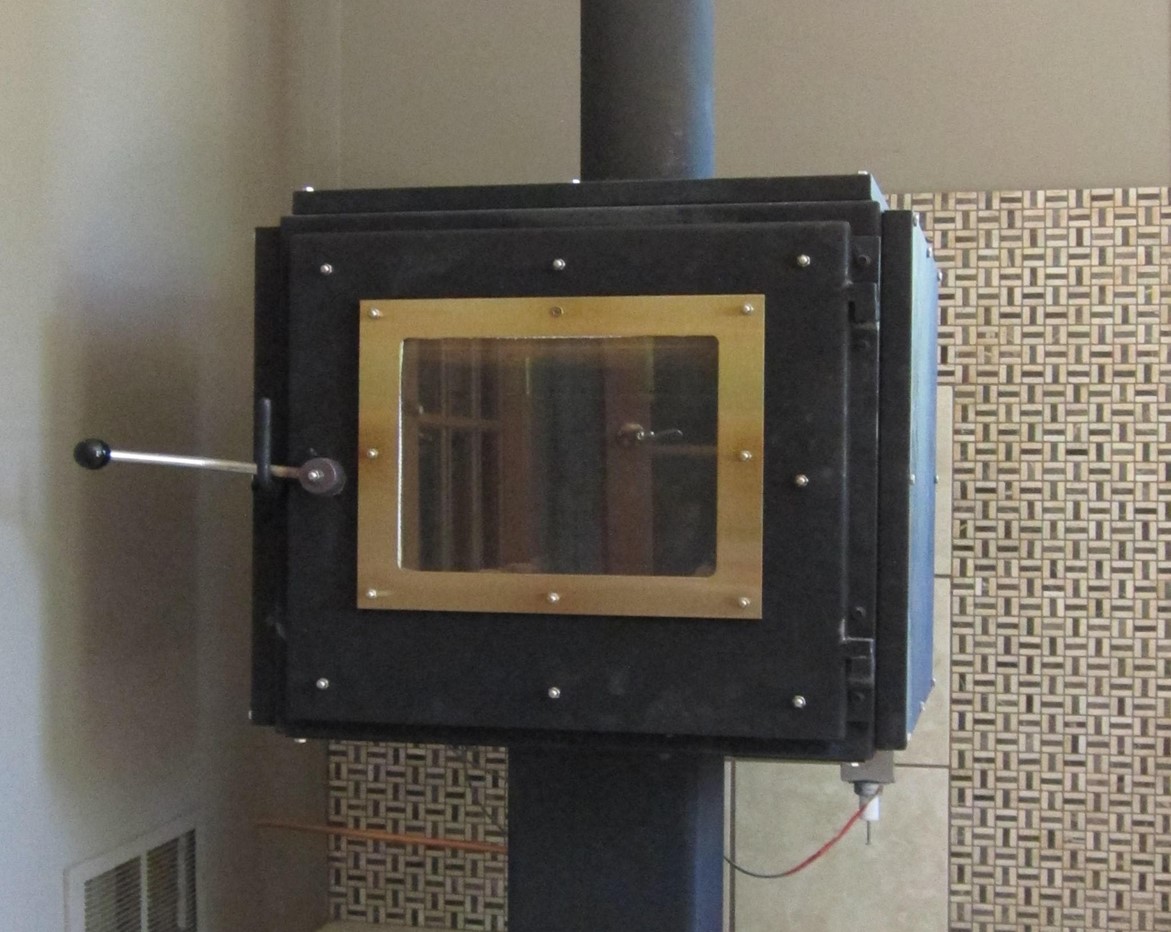
The Problem: Woodstoves have always been somewhat inefficient and smoky. Now that there are more of them it’s time for engineers to do just what they did for internal combustion engines in cars 50 years ago: use computers to maintain a clean burn, adding catalysts and improving combustion chambers.
The Technology: The OmniBurn heater uses smart computer algorithms to optimize the entire combustion process. It also adapts the optimization to include the effects of the flue and the type, shape, and moisture content of the fuel. It has two computer-controlled air valves instead of the usual one. It has a large and effective heat exchanger, a mass airflow sensor, and an exhaust gas temperature sensor. What differentiates this heater is the computer code which is the result of more than 10 years of development and testing. This heater has also been “designed for manufacture” from the very beginning. Constructing the stove only requires about 200 lbs of metal and less than $200 (prototype quantities) of glass, and electronics. This heater should be able to be produced in quantity very inexpensively.
The Team: Jack Kleiss, Jr has degrees from Carnegie Mellon University and George Washington University and was employed in the field of nuclear and combustion energy. He worked for the Westinghouse Nuclear Division and developed controls for the next generation engines for helicopters.
Contact: Jack Kleiss, jackkleissjr.ta@gmail.com
MF Fire
Baltimore, MD
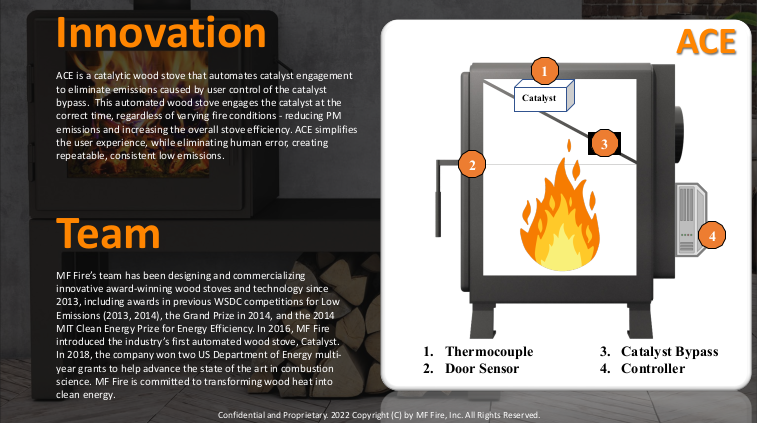
The Problem: Catalysts are essential parts of many clean burning wood stoves but unlike cars, they need to be manually engaged by the user after they warm up and users frequently engage them too early, too late, or not at all.
The Technology: MF Fire will solve this problem of sub-optimally timed catalyst engagement through a new and novel wood heater called ACE. ACE automates catalyst engagement to eliminate emissions caused by poor manual stove operations and deliver an efficiency greater than 75%. ACE is designed to attack and lower all sources of emissions contribution while improving efficiencies when burning wood.
The Team: MF Fire is an award-winning company started by engineering students at the University of Maryland in 2013. Its team members have designed and commercialized numerous innovative EPA compliant wood stoves. They won awards in the 2013 Wood Stove Decathlon and 2014 Wood Stove Design Challenge and the 2014 MIT Clean Energy Prize for Energy Efficiency.
Contact: Paul LaPorte, paul@mffire.com. Web: www.mffire.com
Stanford University
Los Angeles, CA
The Problem: The demographic that relies on wood as a primary heating fuel are often economically challenged households. The target
unit price is $500 with installation costing less than $500.
The Technology: The Stanford Smokeless Stove has a countercurrent heat exchanger in an insulated chamber within the exhaust stream.
This generates and maintains a self-sustaining hot spot in the exhaust stream. Organic particulates passing through this hot spot are fully
combusted to CO2 and H2O eliminating particulates in the exhaust. Additional heat is harvested from the combustion of the particulates maximizing
fuel efficiency. The volume of noxious emissions in the exhaust is inversely proportional to burn rate. Low overnight burn rates, common in
American heater use, conserve fuel but release abundant, noxious, energy-rich emissions. Our afterburner fixes this issue.
The Team: Dr. Heller has been a professor of biology at Stanford since 1972 and has worked on many aspects of thermoregulatory
physiology in animals and humans. Dr. Grahn is the inventor of the afterburner technology and holds 15 patents for heat exchange technologies.
He was the winner of the Puget Sound Clean Air Agency Woodstove Retrofit Challenge. Dr. Lynn Hildemann, also at Stanford, is a collaborator on
the project bringing her strong research background and proven track record in aerosol science related projects to the team.
Contact: Dr. Heller, hcheller@stanford.edu. Web: https://biology.stanford.edu.
The Problem: The demographic that relies on wood as a primary heating fuel are often economically challenged households. The target unit price is $500 with installation costing less than $500.
The Technology: The Stanford Smokeless Stove has a countercurrent heat exchanger in an insulated chamber within the exhaust stream. This generates and maintains a self-sustaining hot spot in the exhaust stream. Organic particulates passing through this hot spot are fully combusted to CO2 and H2O eliminating particulates in the exhaust. Additional heat is harvested from the combustion of the particulates maximizing fuel efficiency. The volume of noxious emissions in the exhaust is inversely proportional to burn rate. Low overnight burn rates, common in American heater use, conserve fuel but release abundant, noxious, energy-rich emissions. Our afterburner fixes this issue.
The Team: Dr. Heller has been a professor of biology at Stanford since 1972 and has worked on many aspects of thermoregulatory physiology in animals and humans. Dr. Grahn is the inventor of the afterburner technology and holds 15 patents for heat exchange technologies. He was the winner of the Puget Sound Clean Air Agency Woodstove Retrofit Challenge. Dr. Lynn Hildemann, also at Stanford, is a collaborator on the project bringing her strong research background and proven track record in aerosol science related projects to the team.
Contact: Dr. Heller, hcheller@stanford.edu. Web: https://biology.stanford.edu.
Stony Brook University
Stony Brook, NY
The Problem: A significant portion of the emissions from woodstoves is due to incomplete combustion because of poor air charge
mixing, low chamber temperatures, low residence times of the fuel/air mixture, and/or an overall lack of available oxygen. Modern stoves
are greatly improved, but tend work well under very specific operating conditions, which are often deviated from due to user error and
other factors.
The Technology: The AIMS, developed by the Stony Brook team incorporates a minimal set of measurement sensors and a heuristic
control strategy for the variable and intelligent introduction of combustion air. The sensor data, calculated performance metrics, actuation,
and overall logic controls are determined using a low-cost microprocessor (Raspberry Pi) that will identify the combustion regime, and
strategy (reduction/maximization of combustion air) that will be utilized to improve efficiency and reduce emissions. An additional benefit
of logging historical operational data can allow for the recommendation of sensor replacement and user feedback based on historical values.
If external power for the sensors and controls is not available, the device defaults back to manual mode. Suggestions for the size and timing
of additional fuel charge may also be made based on the conditions of the stove at the specified refueling.
The Team: The Stony Brook University team, led by Prof. Dimitris Assanis, has significant experimental and computational combustion
experience. Members also include Prof. Jon Longtin and doctoral students Jason Loprete and Mahmoud Koraïem.
Contact: Dimitris Assanis, dimitris.assanis@stonybrook.edu. Web: https://you.stonybrook.edu/combustion
The Problem: A significant portion of the emissions from woodstoves is due to incomplete combustion because of poor air charge mixing, low chamber temperatures, low residence times of the fuel/air mixture, and/or an overall lack of available oxygen. Modern stoves are greatly improved, but tend work well under very specific operating conditions, which are often deviated from due to user error and other factors.
The Technology: The AIMS, developed by the Stony Brook team incorporates a minimal set of measurement sensors and a heuristic control strategy for the variable and intelligent introduction of combustion air. The sensor data, calculated performance metrics, actuation, and overall logic controls are determined using a low-cost microprocessor (Raspberry Pi) that will identify the combustion regime, and strategy (reduction/maximization of combustion air) that will be utilized to improve efficiency and reduce emissions. An additional benefit of logging historical operational data can allow for the recommendation of sensor replacement and user feedback based on historical values. If external power for the sensors and controls is not available, the device defaults back to manual mode. Suggestions for the size and timing of additional fuel charge may also be made based on the conditions of the stove at the specified refueling.
The Team: The Stony Brook University team, led by Prof. Dimitris Assanis, has significant experimental and computational combustion experience. Members also include Prof. Jon Longtin and doctoral students Jason Loprete and Mahmoud Koraïem.
Contact: Dimitris Assanis, dimitris.assanis@stonybrook.edu. Web: https://you.stonybrook.edu/combustion
Wittus
Pound Ridge, NY
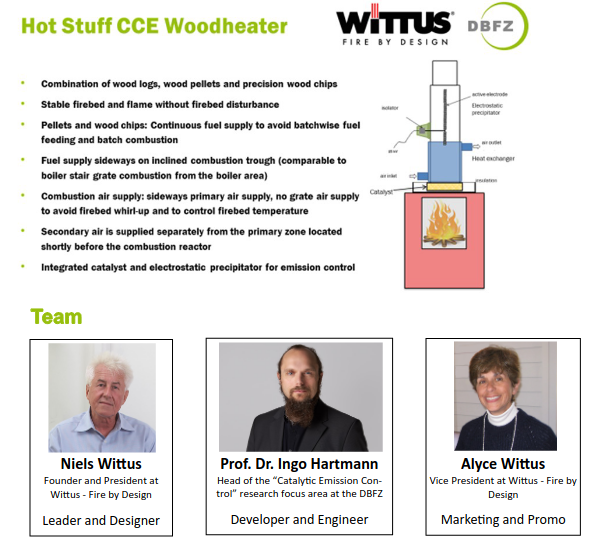
The Problem: Many consumers want the benefits of both wood and pellet heating but must decide between the two and they often default to more polluting wood heaters. Higher prices for pellets and intermittent pellet shortages also depress cleaner pellet heater deployment:
The Technology: The HotStuff woodheater can use wood logs, wood pellets or wood chips. The firebox design enables a stable fire bed and thus continuous combustion. The combustion air supply is divided into primary and secondary zones. Secondary air is supplied separately and immediately as the gases enter the secondary reaction zone. The HotStuff heater is equipped with a combustion chamber-integrated catalytic converter and an integrated electrostatic precipitator and can have a water heat exchanger for heat utilization in rooms adjacent to the heater and for storing the heat in a buffer tank. At a firing capacity of 4 kW, particulate mass flows of less than 0.15 g/h can be achieved for beech chips, spruce chips and wood pellets.
The Team: Niels Wittus is the Founder and President at Wittus - Fire by Design, an importer, developer, and distributor of wood and gas stoves since 1978. Alyce Wittus, is a VP at Wittus has worked with labs on UL/ULC and EPA testing. Professor Dr. Ingo Hartmann is head of the research focus area “Catalytic Emission Control” at the German Biomass Research Centre.
Contact: Niels Wittus, nw@wittus.com. Web: https://wittus.com
Woodgas Pyrolytics
Normal, IL
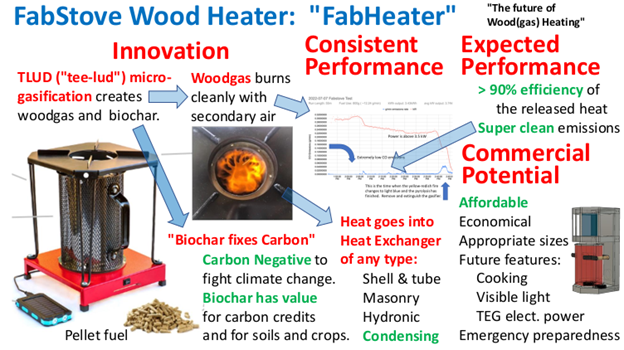
The Problem: Wood smoke exposure is an indoor health hazard for hundreds of millions of people who cook with wood-fueled fires around the globe. One proven solution, the TLUD stove, can also be adapted to indoor vented heating and cooking in the United States at rock bottom prices.
The Technology: The Fabstove Room Heater provides clean heat via pyrolytic micro-gasification of pellet fuel. Our focus is on small amounts of heat to secure basic comfort and emergency preparedness. The TLUD ( “tee-lud”) technology entails a top-lit fire that creates a downward “migratory pyrolytic front” in a column of fuel sustained by a controlled updraft of primary air. The created woodgas moves upward for combustion with separately entering secondary air. This is a true gas-burning stove that creates its own gases from solid biomass fuel. Additionally, carbon negative cooking (and room heating) is achieved because fifty percent (50%) of the carbon atoms of the biomass fuel remain in the stove as charcoal, a co-product that becomes biochar when sequestered in soils. Fabstove Room Heaters (FabHeaters) are fan assisted TLUD devices that have been fitted with heat exchangers and external venting.
The team: Paul Anderson, PhD, owner and CEO of Woodgas Pyrolytics, Inc., is an internationally recognized leader (“pyroneer”) and expert in TLUD technology and applications, especially cookstoves. David Lello, owner and CEO of Ekasi Energy Ltd (South Africa) is an accomplished businessman and product developer.
Contact: Paul Anderson, psanders@ilstu.edu. Web: www.woodgas.com.