Exploring Blended Materials Along Compositional Gradients
A new platform for rapidly creating and characterizing blends of polymers, nanoparticles, and other materials could significantly accelerate material development
November 24, 2020
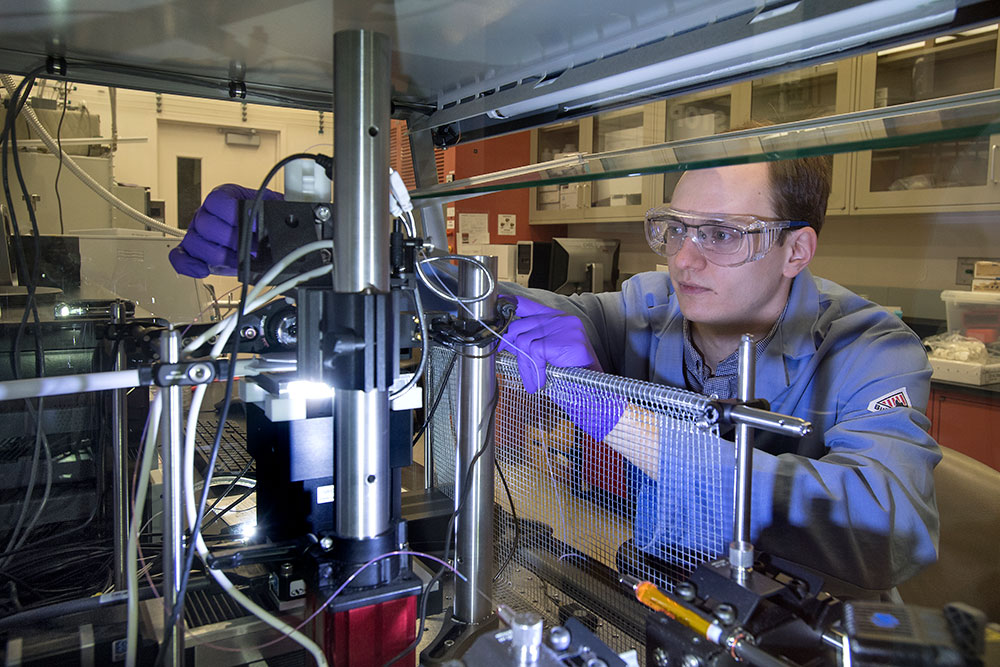
Yale University PhD student Kristof Toth (pictured above) with the electrospray deposition tool he designed, built, and validated in collaboration with staff scientist Gregory Doerk of Brookhaven Lab's Center for Functional Nanomaterials (CFN). This CFN tool allows users to blend multiple components—such as polymers, nanoparticles, and small molecules—over a range of compositions in a single sample. Next door to the CFN, at the National Synchrotron Light Source II, users can probe how the structure of the blended material changes across this entire composition space.
UPTON, NY—Blending is a powerful strategy for improving the performance of electronics, coatings, separation membranes, and other functional materials. For example, high-efficiency solar cells and light-emitting diodes have been produced by optimizing mixtures of organic and inorganic components.
However, finding the optimal blend composition to produce desired properties has traditionally been a time-consuming and inconsistent process. Scientists synthesize and characterize a large number of individual samples with different compositions one at a time, eventually compiling enough data to create a compositional “library.” An alternative approach is to synthesize a single sample with a compositional gradient so that all possible compositions can be explored at once. Existing combinatorial methods for rapidly exploring compositions have been limited in terms of the types of compatible materials, the size of compositional increments, or number of blendable components (often only two).
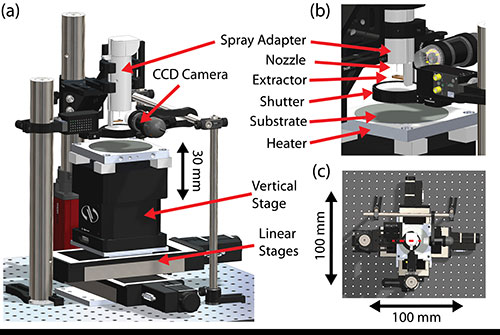
A schematic of the electrospray deposition tool (a), with zoomed-in (b) and aerial (c) views.
To overcome these limitations, a team from the U.S. Department of Energy’s (DOE) Brookhaven National Laboratory, Yale University, and University of Pennsylvania recently built a first-of-its-kind automated tool for depositing films with finely controlled blend compositions made of up to three components onto single samples. Solutions of each component are loaded into syringe pumps, mixed according to a programmable “recipe,” and sprayed as tiny electrically charged droplets onto the surface of a heated base material called a substrate. By programming the flow rates of the pumps as a stage underneath the substrate changes position, users can obtain continuous gradients in composition.
Now, the team has combined this electrospray deposition tool with the structural characterization technique of x-ray scattering. Together, these capabilities form a platform to probe how material structure changes across an entire composition space. The scientists demonstrated this platform for a thin-film blend of three polymers—chains made of molecular building blocks linked together by chemical bonds—designed to spontaneously arrange, or “self-assemble,” into nanometer-scale (billionths of a meter) patterns. Their platform and demonstration are described in a paper published today in RSC Advances, a journal of the Royal Society of Chemistry (RSC).
“Our platform reduces the time to explore complex compositional dependencies of blended material systems from months or weeks to a few days,” said corresponding author Gregory Doerk, a staff scientist in the Electronic Nanomaterials Group at Brookhaven Lab’s Center for Functional Nanomaterials (CFN).
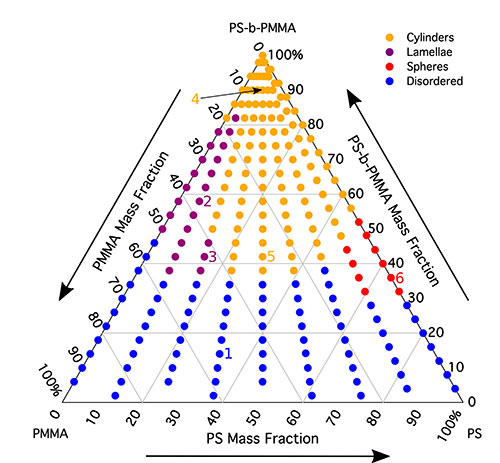
The morphology diagram derived from the x-ray scattering data shows where in the composition space the cylinders, lamellae (vertical sheets), spheres, and disorder occur. Pure PS-PMMA block copolymer is located at the top of the triangle, and pure PMMA and PS homopolymers are at the lower left and right of the triangle, respectively. Each colored point represents a single x-ray measurement (the numbered points correspond to measurements described in detail in the paper).
“We constructed a morphology diagram with more than 200 measurements on a single sample, which is like making 200 samples the conventional way,” said first author Kristof Toth, a PhD student in the Department of Chemical and Environmental Engineering at Yale University. “Our approach not only reduces sample preparation time but also sample-to-sample error.”
This diagram mapped how the morphologies, or shapes, of the blended polymer system changed along a compositional gradient of 0 to 100 percent. In this case, the system contained a widely studied self-assembling polymer made of two distinct blocks (PS-b-PMMA) and this block copolymer’s individual block constituents, or homopolymers (PS and PMMA). The scientists programmed the electrospray deposition tool to consecutively create one-dimensional gradient “strips” with all block copolymer at one end and all homopolymer blend at the other end.
To characterize the structure, the team performed grazing-incidence small-angle x-ray scattering experiments at the Complex Materials Scattering (CMS) beamline, which is operated at Brookhaven’s National Synchrotron Light Source II (NSLS-II) in partnership with the CFN. In this technique, a high-intensity x-ray beam is directed toward the surface of a sample at a very low angle. The beam reflects off the sample in a characteristic pattern, providing snapshots of nanoscale structures at different compositions along each five-millimeter-long strip. From these images, the shape, size, and ordering of these structures can be determined.
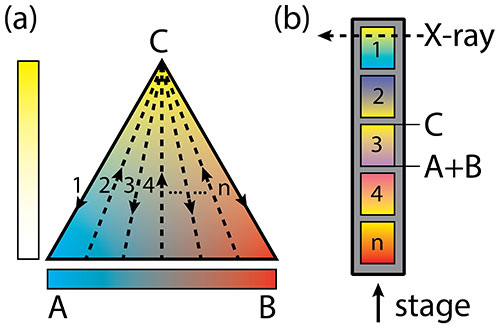
Each deposited strip is a gradient from block copolymer (C) to homopolymer blend (A+B) on a single substrate. Within each strip, the homopolymer blend is maintained at a constant PS (B) to PMMA (A) ratio.
“The synchrotron’s high intensity x-rays allow us to take snapshots at each composition in a matter of seconds, reducing the overall time to map the morphology diagram,” said co-author Kevin Yager, leader of the CFN Electronic Nanomaterials Group.
The x-ray scattering data revealed the emergence of highly ordered morphologies of different kinds as the blend composition changed. Normally, the block copolymers self-assemble into cylinders. However, blending in very short homopolymers resulted in well-ordered spheres (increasing amount of PS) and vertical sheets (more PMMA). The addition of these homopolymers also tripled or quadrupled the speed of the self-assembly process, depending on the ratio of PS to PMMA homopolymer. To further support their results, the scientists performed imaging studies with a scanning electron microscope at the CFN Materials Synthesis and Characterization Facility.
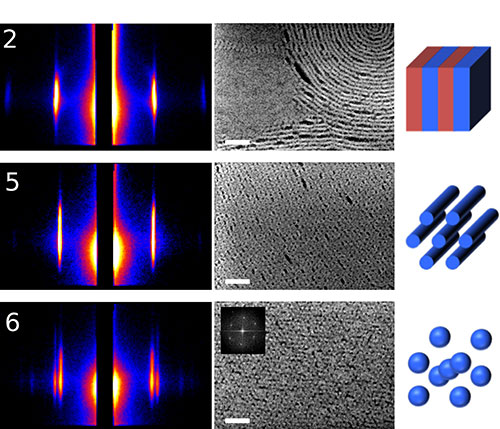
X-ray scattering patterns (left) with corresponding scanning electron microscope (SEM) images (middle) and morphology schematics (right) for selected numbered points in the morphology diagram. Vertical sheets occur at point 2, cylinders at point 5, and spheres at point 6. The scale bars in the SEM images indicate a length of 200 nanometers.
Though the team focused on a self-assembling polymer system for their demonstration, the platform can be used to explore blends of a variety of materials such as polymers, nanoparticles, and small molecules. Users can also study the effects of different substrate materials, film thicknesses, x-ray beam focal spot sizes, and other processing and characterization conditions.
“This capability to survey a broad range of compositional and processing parameters will inform the creation of complex nanostructured systems with enhanced or entirely new properties and functionalities,” said co-author Chinedum Osuji, the Eduardo D. Glandt Presidential Professor of Chemical and Biomolecular Engineering at the University of Pennsylvania.
In the future, the scientists hope to create a second generation of the instrument that can create samples with mixtures of more than three components and which is compatible with a range of characterization methods—including in situ methods to capture morphology changes during the electrospray deposition process.
“Our platform represents a huge advance in the amount of information you can get across a composition space,” said Doerk. “In a few days, users can work with me at the CFN and the beamline staff next door at NSLS-II to create and characterize their blended systems.”
“In many ways, this platform complements autonomous methods developed by CFN and NSLS-II scientists to identify trends in experimental data,” added Yager. “Pairing them together has the potential to dramatically accelerate soft matter research.”
This work was funded by the DOE Office of Science and National Science Foundation. The CFN and NSLS-II are DOE Office of Science User Facilities.
CFN facilities are available free of charge to scientists from universities, industry, and national laboratories worldwide. If you are interested in using the new electrospray deposition tool for your research, submit a proposal. The next deadline is January 31, 2021. If you have questions about the CFN user program, please contact CFN User Program Administrator and Outreach Coordinator Grace Webster at (631) 344-3227 or gwebster@bnl.gov. For questions about using CFN facilities or partnering with CFN scientists, please contact CFN Assistant Director for Strategic Partnerships Priscilla Antunez at (631) 344-6186 or pantunez@bnl.gov.
Brookhaven National Laboratory is supported by the U.S. Department of Energy’s Office of Science. The Office of Science is the single largest supporter of basic research in the physical sciences in the United States and is working to address some of the most pressing challenges of our time. For more information, visit https://energy.gov/science.
Follow @BrookhavenLab on Twitter or find us on Facebook.
2020-17172 | INT/EXT | Newsroom