Automating 2-D Material Exfoliation with Suji Park
interview with a CFN staff researcher
September 22, 2020
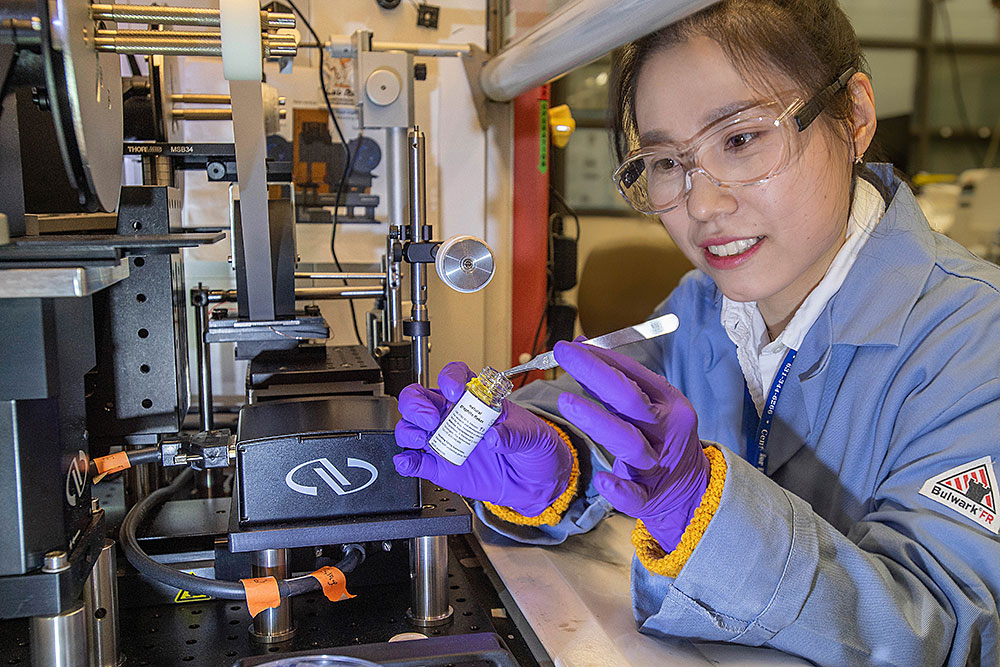
Suji Park picks up particles of graphite—a form of crystalline carbon—to put them on a roller for depositing source materials. This roller is part of a semi-automated system Park built to exfoliate ultrathin 2-D materials from 3-D "parent" materials. In this case, graphite (3-D) will be exfoliated to generate graphene (2-D). The exfoliator will become part of the Quantum Material Press (QPress), an automated machine under development that consists of modules for making atomically thin 2-D materials and stacking them into layered structures with new properties. As the different modules are built, they will become available to users in the Materials Synthesis and Characterization Facility at Brookhaven Lab's Center for Functional Nanomaterials.
Suji Park is a scientific associate in the Electronic Nanomaterials Group at the Center for Functional Nanomaterials (CFN), a U.S. Department of Energy (DOE) Office of Science User Facility at Brookhaven National Laboratory. Since joining the CFN in October 2019, she has been designing and building hardware for the automated exfoliation of high-quality atomically thin “flakes” from 3-D bulk materials. When these 2-D material flakes are stacked into layered structures, new electrical, optical, magnetic, and other properties can emerge. Such 2-D heterostructures could find applications in areas including catalysis, solar energy, and quantum computing. Park received a bachelor’s degree and PhD in materials science and engineering from Pohang University of Science and Technology in South Korea. She then went on to do three postdocs—one at a neutron imaging facility at the Korea Atomic Energy Research Institute, another in Stanford’s Chemical Engineering Department, and a third at the Stanford Institute for Materials and Energy Sciences at SLAC National Accelerator Laboratory.
What characterizes 2-D materials, and why are scientists interested in them?
2-D materials are ultrathin. They are just a few atoms thick—or even just a single atom thick! The most well-known 2-D material is graphene, which is made of sheets of carbon exfoliated from graphite. The different layers of graphite are held together by weak forces, making them easy to detach. This is why we can make 2-D single-layer flakes of graphene. By stacking flakes from different materials, we can create layered structures that are essentially new materials. This lets us tune their mechanical, optical, and electrical properties. There are exciting theoretical predictions for making quantum devices based on 2-D materials, but the bottleneck is actually making these layered materials.
Why is flake fabrication so challenging?
The traditional way to make 2-D materials is through mechanical exfoliation. Adhesives are repeatedly attached to and detached from a bulk crystal so that the fragments get thinner and thinner. When the materials become thin enough, the adhesives are pressed into silicon wafers to transfer the flakes onto the wafer surface. Eventually, you end up with some very small-sized monolayers.
However, the mechanics of this exfoliation process are not very well understood. This process is laborious, has very low reproducibility, and the quality of the flakes strongly depends on who is performing the exfoliation. Because of the lack of understanding, controlling the size, shape, and other parameters of the flakes is quite difficult. People spend a lot of time to get just one perfect flake. Then, they have to repeat this process many times to build complex layered structures.
Graphene was discovered in 2004. Why is our understanding of exfoliation mechanics still limited after all these years?
This has been a question of mine, too. When I began researching mechanical exfoliation, I found that many scientists have simulated how mechanical exfoliation works. However, these results are limited in terms of their applicability to real-world material performance.
Systematic experiments, in which all variables are carefully controlled, are difficult to perform because exfoliation has multiple steps. For example, if I have three possible variables—pressure, temperature, and speed—and I want to find out how speed affects the exfoliation process, I would fix the temperature and pressure and test the process for selected speeds. But for manual exfoliation, it’s not really possible to fix, or even to measure, the peeling speed. You can’t really ask a scientist to peel at a precise speed. This is a limitation of relying on human hands to make materials. Moreover, we lack statistical methods to analyze exfoliated flakes, which are difficult to see and characterize from images.
From an engineering standpoint, reproducibility and reliability are very important. Automation can help by minimizing human engagement. These factors are the motivation behind the automated 2-D material sample preparation system that I’m building to generate consistent, high-quality flakes.
What is involved in building this automated system?
When I joined the CFN, a prototype exfoliator already existed as part of the first generation of a larger automated machine called the QPress, or Quantum Material Press. This exfoliator used a stamp made of a polymer (PDMS) instead of a tape to perform basic robotic motions such as pushing and pulling.
First, I wanted to understand the factors important to mechanical exfoliation. By understanding this process, I can start to control it. I began by studying pressure-sensitive adhesives, which are adhesive tapes that stick to surfaces via applied pressure, and the theoretical background of mechanical exfoliation, step by step. I found that there are factors that we can control, such as pressure, temperature, and dwell time (how long the tape is adhered on a surface). But what is the appropriate amount of pressure? How long do we need to apply that pressure? What kind of pressure application is better—pushing or rolling? Answering such questions is the first step of automation.
To start, I upgraded the QPress exfoliator with functions to quantitatively control the temperature and pressure with various adhesives. With this setup, I could fulfill basic tests for each of these parameters and find specifications required for automation. I also tested the idea of using a roller instead of a stamp to apply pressure, temperature, and rolling speed at the same time. I tried a commercial laminator, and it actually worked! This test opened a new direction for us to consider for the automation process.
More recently, I came up with a new design for a fully automated roll-to-roll (R2R) exfoliator, relying on the knowledge I gained from my early experiments. On the basis of this design, I built a semi-automated R2R exfoliator. With this setup, I can do systematic research to better understand the underlying mechanisms of mechanical exfoliation and find optimized conditions.
As I explained, mechanical exfoliation is simply a combination of two steps: attachment and detachment, or peeling, of adhesives. With the early push-and-pull type of exfoliator, I could focus on the first step. However, the second step is as critical as the first. Using the R2R exfoliator, I want to control and compare important parameters in the detachment process besides temperature, pressure, and rolling speed (or dwell time). One parameter is the peeling speed and angle. For example, if you peel the tape at 45 instead of 90 degrees, the peeling force changes.
How does the R2R exfoliator work?
The R2R exfoliator has several components. A motorized tape unwinder continuously supplies bare pressure-sensitive adhesive tape from a reel. The tape runs over a roller for source material deposition, picking up the source materials. The tape with the source particles is located under a press roller. A sample stage moves to the left, and the roller compresses the source materials at a pressure similar to that of manual exfoliation. After the materials are compressed, we bake the sample using a heating plate installed in the sample stage. Finally, we move the sample stage to the right. The combined motion of a tape rewinder and the sample stage causes the compressed tape to peel off the sample surface. We can control the peeling speed with the sample stage and the peeling angle with an angle adjustment roller.
What excites you most about studying a process that is still not well understood?
Through my research, I am building an entirely new facility with unique capabilities. I am starting from a very basic understanding, progressing step by step. My role is to integrate the incremental findings and complete a big puzzle in my own creative way. It is challenging, but small improvements in understanding fundamental steps in 2-D materials fabrication will allow us to move forward and eventually complete the whole system. This system will help other researchers save time, effort, and research funds and support the creation of new 2-D materials that could be used in our daily lives. Contributing to society in this way makes me feel very good.
Which materials are you using for the tape and which 2-D materials are you exfoliating? Are the 2-D materials limited to those of interest for quantum information science, as the QPress name suggests?
For the purpose of machine development, I am currently using a simple commercial tape, the same that you would use in any office setting. Using commercial tapes is nice because we can easily test different kinds of adhesives. For instance, I am also studying wafer dicing tapes that are used in the semiconductor industry because they leave less residue on the wafer surface after exfoliation.
For 2-D material exfoliation, my current target is graphene because it is the most widely studied. The project team is also trying to produce high-quality flakes from materials for which it is hard to obtain such high quality—for example, very brittle materials. Team member Young-Jae Shin is an expert in 2-D materials. With the commercial laminator, he has been testing molybdenum disulfide and tungsten disulfide, which are more brittle than graphene. I will test these materials with the R2R exfoliator after I finish testing graphene.
Our goal is to help users exfoliate any materials that interest them. The QPress project was initially started with quantum materials in mind, given the recent emphasis on quantum information science research. However, the machine will be available to users who are looking to generate any kind of 2-D materials. Because the machine can run 24 hours a day, it saves a lot of time in generating flakes. Also, we’re planning to make a library-type database of different flakes that users can access for their research.
You mentioned that the exfoliator will be part of a larger automated machine, the QPress. Are you only working on the exfoliation component?
The final QPress will have robot arms that transfer samples from the exfoliator station to cataloger, stacker, and characterization stations. This workflow will be automated. While my main focus so far has been on making the exfoliator, I’m also working on designing an automated setup for the stacker and figuring out how to combine these different modules. Achieving full automation could be difficult because different tools have different requirements in terms of sample environments, required motions, and physical space. It’s a complicated design issue.
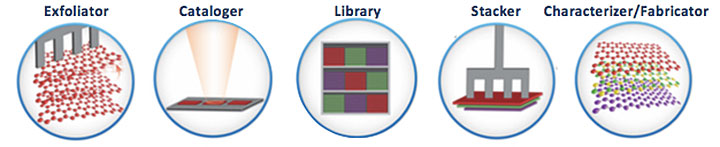
Park is building the first part of the automated system for 2-D materials generation: the exfoliator. The exfoliator will enable the design of systematic experiments with precisely controlled environments. The other modules are a cataloger to record the locations and properties of exfoliated flakes, a library containing a database of 2-D flakes, a stacker that picks flakes up and stacks them into layers, and a characterizer that will identify the crystal structure and orientation of exfoliated flakes and layered materials. Park is also designing an automated workflow to move samples between these modules.
My goals by the end of this year are to complete the fully automated R2R exfoliator, make the R2R exfoliator a functional part of the QPress, and build the first prototype of the automated stacker.
It sounds like building the exfoliator and integrating it into a multicomponent system requires a combination of 2-D materials knowledge and mechanical design expertise. How are you applying your knowledge and experience to this project?
My PhD was in materials science and engineering. For my thesis, I used a synchrotron x-ray microscope to study wetting on polymers. During my postdoc at Stanford, I continued using the synchrotron x-ray microscope to study the fluid dynamics of tear films on soft contact lenses.
When I went to SLAC, I changed my career path. I started studying microstructural changes in solid crystals through ultrafast electron diffraction. I was slightly involved in 2-D material studies, mostly on the experimental side rather than data analysis. Because I was a joint postdoc at Stanford and SLAC, my role was split between maintenance and user support of the electron diffraction facility and my own research. I was frequently involved in the development of new functions at the facility. For example, I designed an upgraded version of a vacuum chamber and manipulator system. So, over the years, I have become used to diving into new areas. As a result, I’m more open-minded and less fearful of taking on new and challenging projects.
Though my field of expertise is not 2-D materials, my unique background in materials science, fluid mechanics, and soft-matter physics and my hands-on experience is very useful in terms of building a facility for 2-D material exfoliation. For example, the adhesives used in mechanical exfoliation are polymers. What I researched during my PhD is the wetting property of polymers, or how they contact liquid surfaces. The exfoliation process is related to wetting but for solid flakes instead of liquids. So, I can apply my expertise related to the mechanics to understand interface phenomena between adhesives and flakes.
What led you to pursue studies in materials science and engineering and a career in scientific research?
I have liked science and math my entire life. Initially, I wanted to be a high school math teacher. But I realized that being a scientist was more aligned with my goal of making a general impact on the world. I chose materials science because materials are the fundamental elements accelerating technology development. I’m very excited to see what 2-D materials emerge from the QPress and how they are applied to new technologies.
Interested in using QPress capabilities at the CFN? Submit a user proposal through the online proposal system. The next deadline is September 30. If you have questions about becoming a CFN user or partnering with Park or other CFN scientists, please contact CFN Assistant Director for Strategic Partnerships Priscilla Antunez at (631) 344-6186 or pantunez@bnl.gov.
Brookhaven National Laboratory is supported by the U.S. Department of Energy’s Office of Science. The Office of Science is the single largest supporter of basic research in the physical sciences in the United States and is working to address some of the most pressing challenges of our time. For more information, visit https://energy.gov/science.
Follow @BrookhavenLab on Twitter or find us on Facebook.
2020-17449 | INT/EXT | Newsroom