Chiral Materials and Unconventional Superconductivity Group
Introduction: Second generation (2G) Y-Ba-Cu-O coated conductor
The second generation (2G) wire is a fundamentally different technology than 1G, the key element being a high-performance 1-2 micron thin YBCO epitaxial layer deposited on a bi-axially textured oxide buffered metal tape. The 2G technology has two key components: (1) a textured template that enables the growth of the biaxially aligned YBCO and (2) the superconducting YBCO layer. Here YBCO stands for the well-known high temperature superconductor YBa2Cu3O7 with Tc = 91 K. Two major approaches used for the textured template include (1) the IBAD process based on the ion beam assisted deposition of a textured oxide layer (i.e., YSZ, GZO, MgO) on a metallic substrate, (2) the RABiTS process based on the deformation and recrystallization texturing of a metal substrate followed by deposition of oxide buffer. The two primary approaches for deposition of the YBCO layers include (1) metal organic deposition (MOD); (2) metal organic chemical vapor deposition (MOCVD). 2G tape is currently produced in U.S. by American Superconductor Corporation who is using RABiTS substrate and deposits YBCO layer by MOD, and SuperPower Inc. (now subsidiary of Phillips Corp.) who is using IBAD (substrate) -MOCVD (YBCO layer) combination.
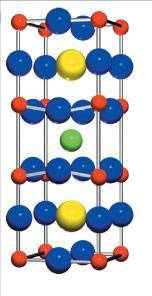
Structure of YBCO material
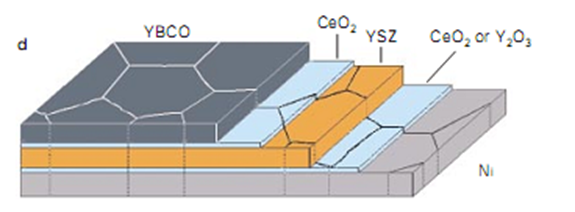
Architecture of 2G wire produced American Superconductor Corporation. YBCO layer is deposited on buffered Ni alloy tape by metal-organic deposition.
2G research started in Brookhaven in 1997 as a collaboration with Oxford Superconductor. The project goal was evaluation of the ex-situ technology for large scale production of thick YBCO film with Jc over 1 MA/cm2. An important milestone was synthesis 5 micron thick layers with Jc over 1 MA/cm2 [1]:
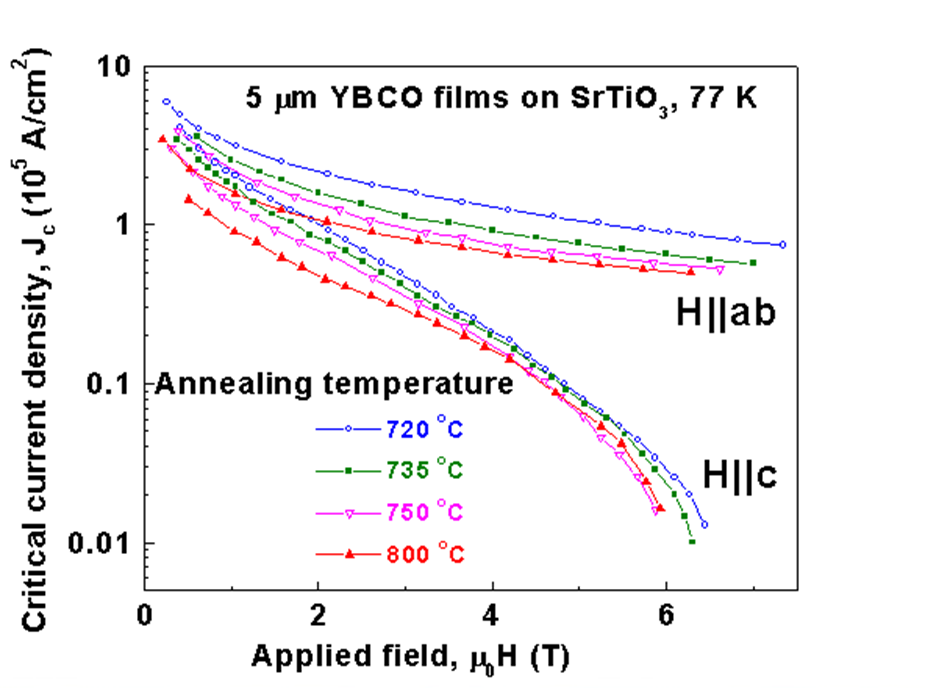
Critical current of 5 micron (record-thickness) YBCO films synthesized at BNL in 1998. The result validated ex-situ technology and promoted wide-spread adoption of the process by the industry.
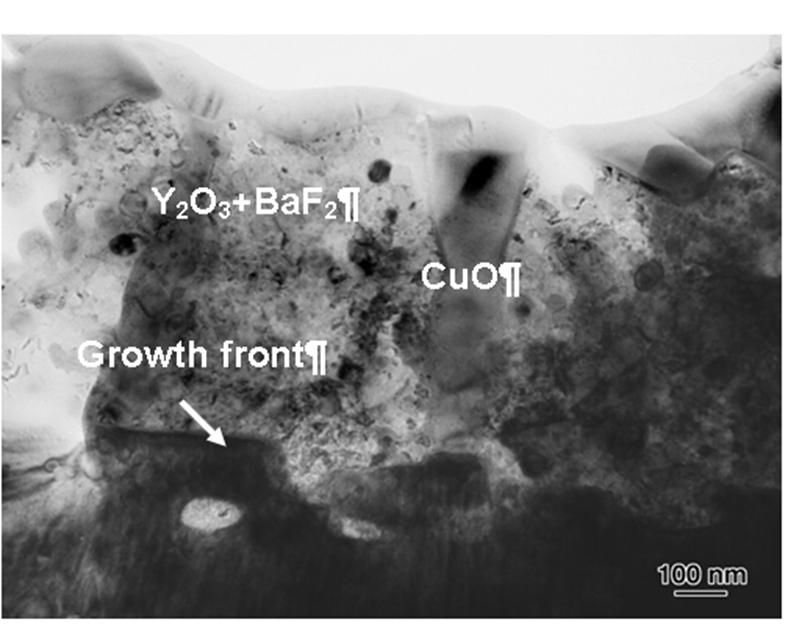
TEM study of the growth process enable optimization of the YBCO layers properties 1997-2000.
Our work on basic thermodynamics of the ex-situ conversion reaction resulted in a discovery of universal law for the reaction rate [2]. An important event was discovery of rate enhancement at low pressure [3]. The discovery was put to practice as patented design of sub-atmospheric reactor. Without low-pressure process the ex-situ reactors would be extremely slow and very expensive to run.
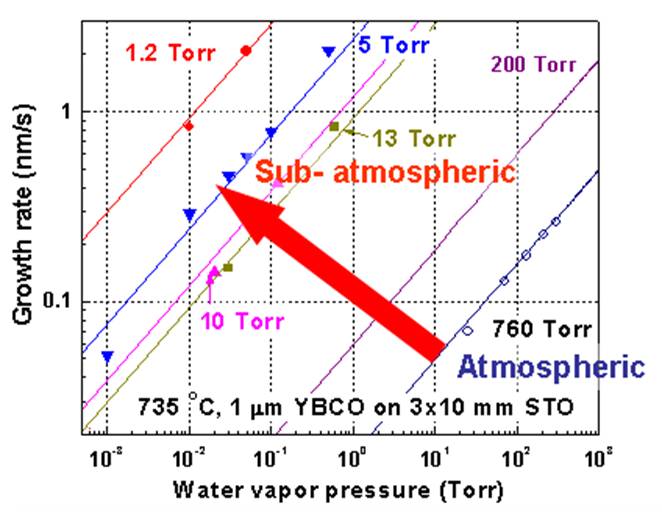
Significant YBCO growth rate can be achieved by reducing total pressure during the ex-situ provessing. This result became a basis for BNL patent # 6,794,339
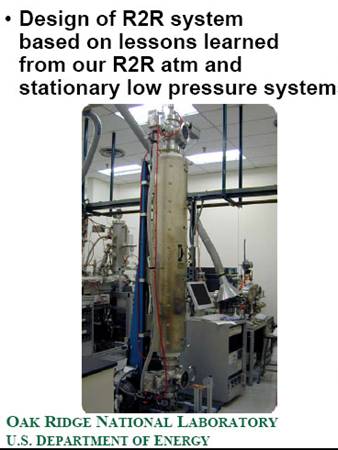
Sub-atmospheric reactor utilizing BNL technology was built at Oak Ridge National Lab for pilot-production of YBCO 2G tapes.
Examples of application of BNL technology:
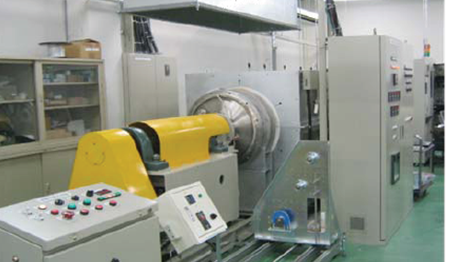
Sub-atmospheric reactor built by Showa Electric Wire and Cable Co., Japan.
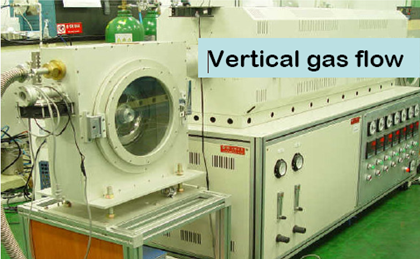
Reactor operating at Institute for Machinery and Materials, Korea.
Reference
- IEEE Transactions on Applied Superconductivity (Proceedings of Applied Supeconductivity Conference ASC 2000), vol. 11, No 1 (March 2001), pp. 2939-2942, “Ex-situ post-deposition processing for large area YBCO films and coated tapes”, V. F. Solovyov, H. J. Wiesmann, L-J. Wu, Y. Zhu, and M. Suenaga.
- Applied Physics Letters, vol. 76, No 14, (April 2000), pp. 1911-1913, “Kinetics of YBa2Cu3O7 film growth by postdeposition processing”, Vyacheslav F. Solovyov, Harold J. Wiesmann, Li-jun Wu, Yimei Zhu, and Masaki Suenaga.
- IEEE Transactions on Applied Superconductivity Superconductivity (Proceedings of Applied Supeconductivity Conference ASC 1998), vol. 9, (June 1999), pp. 1467 - 1470. ”High Rate Deposition of 5 um Thick YBa2Cu3O7 Films Using the BaF2 Ex-situ Post Annealing Process”, V.F. Solovyov, H.J. Wiesmann, L-J. Wu, M. Suenaga and R. Feenstra.
- Applied Physics Letters, vol. 80, No 3 (January 2002), pp. 419-421, "Mechanisms for hetero-epitaxial nucleation of YBa2Cu3O~6.1 at the buried precursor/SrTiO3 interface in the postdeposition reaction process", L. Wu, V. F. Solovyov, H. J. Wiesmann, Y. Zhu, and M. Suenaga.